CNC
If we are to name one thing that has been constant in the manufacturing industry over the years, it would be customers’ need for more sophisticated machining technologies to meet their stringent design and manufacturing requirements. One machining technology that has been helping machinists satisfy these requirements today is the CNC laser cutter.
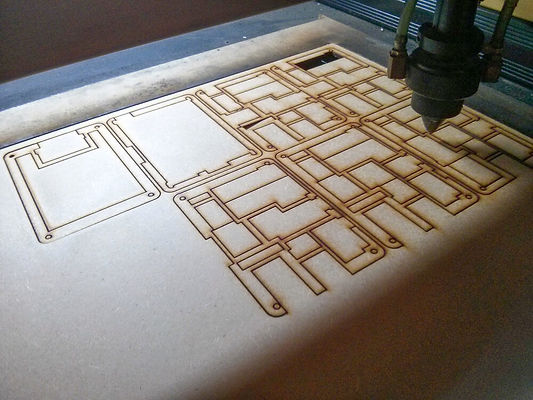
A CNC laser cutter is a piece of computer numerical control (CNC) equipment that uses a focused, high-powered laser beam to mark, cut, or engrave a material to form custom shapes. Its unique design and operation make it highly accurate, especially when cutting intricate shapes and small holes.
First, we will explain the CNC laser cutting process before discussing its types and advantages over conventional CNC machining. Like every other type of CNC machine, a CNC laser cutter relies on computer numerical control and computer instructions (G-code) to perform its sequence of cutting operations. However, CNC laser cutters differ slightly from conventional CNC machines in their design and method of cutting operation.
CNC laser cutting is a non-contact, thermal-based process. A CNC laser cutter features a laser head containing a laser focusing lens and a nozzle. Through the nozzle, this head and lens assembly focuses a laser beam — a column of very high-intensity light ㅡ on the workpiece, melting and cutting the workpiece to form the desired shape. CNC lasers employ compressed gas (also flowing through the nozzle that ejects the laser beam) to cool the focusing lens and expel the vaporized metal out of the workpiece.
Look at it this way. When you focus a high-powered laser beam at a point on a metallic surface, the heat density at that point becomes high, resulting in rapid heating and partial (or complete) vaporization of that point on the metal. CNC technology then controls the sequence of movements of this laser head and laser beam on the work surface to form the desired custom shapes and features.
CNC laser cutters are typically categorized based on the state of the active laser medium (solid, liquid, or gas) and the component of the active laser medium (for example, CO2, Nitrogen, etc.). Here are three of the most commonly used types of lasers today:
-
CNC CO2 laser cutter
-
CNC crystal laser cutter
-
CNC fiber laser cutter
CNC CO2 Laser Cutter
The CO2 laser cutter is a type of gas laser that employs carbon dioxide as the active laser medium. They are the most common type of laser cutters primarily because of their high power output capability and efficiency.
CO2 laser cutters generate a power output of up to 15 kW and an efficiency of up to 30% (the highest of all the gas laser cutters). They are ideal for cutting fine features and acute angles, especially in sheet metals or metals with a thickness of less than 10 mm. Higher powered CO2 laser cutters can also deliver good cut quality on thicker metal surfaces.
CNC Fiber Laser Cutter
FIber laser cutters are a more recent laser technology that uses a bank of diodes to create the beam, which is focused through a fiber-optic cable. Fiber laser cutters allow you to achieve a faster and cleaner cutting process than CO2 laser cutters, especially in materials with a thickness of less than 5 mm.
Although fiber lasers are compatible with a broad range of materials, you must pay special attention to silver.
Silver retains heat from the laser and starts to warp during cutting operations, making it challenging to achieve the desired machined part. As a result, top-tier machine shops typically use a bracket as a heat sink to transfer heat away from the silver workpiece during fiber laser cutting operations.
CNC Crystal Laser Cutter
CNC crystal laser cutters use beams made from crystals like neodymium-doped yttrium aluminum garnet (Nd:YAG) and neodymium-doped yttrium ortho-vanadate (Nd:YVO).
Crystal laser cutters generally have higher intensity (or laser power) than CO2 laser cutters, meaning you can use them to cut through thicker metals. These cutters also have a broad range of material compatibility, including metals, glass, wood, and plastics.
Here is a list of some of the advantages of the CNC laser cutting process over conventional CNC machining processes:
-
CNC laser cutting produces more intricate designs and holes as small as 2 mm with a high degree of accuracy and precision.
-
CNC laser cutting produces cleaner cuts, eliminating the need for additional post-processing (or finishing ) operations.
-
CNC laser cutters eliminate the need for several cutting tools or custom tools, such as in conventional CNC routers and milling machines.
-
The non-contact nature of the laser cutting process decreases the risk of material distortion and material contamination, making them ideal for machining components that will be used in the medical industry.